20. 4月 2020
, ニュース
プロセスコントロールは必須要素
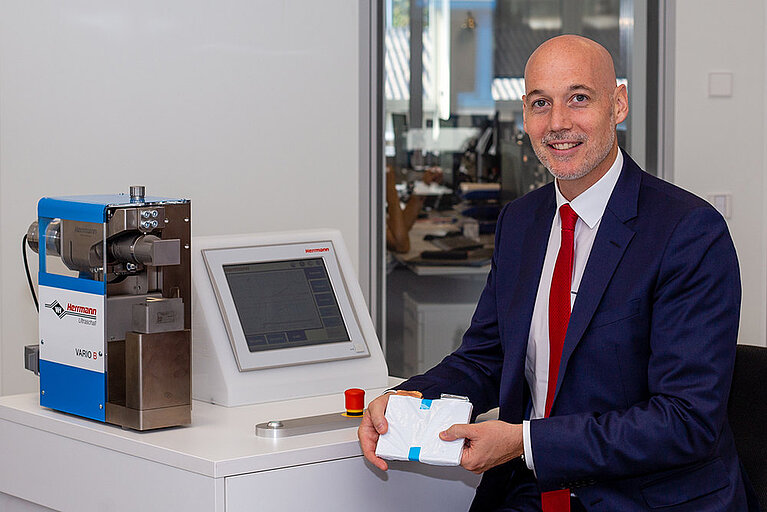
ハーマンは、プラスチック溶着のスペシャリストとして長年活躍されてきました。今、メタル溶着市場に進出されるのはなぜですか?
Thomas Herrmann: プラスチック製品業界のお客様から、金属接合部の溶着に対する要望を受けることが多くなってきました。数十年に及ぶプロセス最適化に関する豊富な経験を金属分野にも応用できるのではないかと考えました。さらに、特にエレクトロモビリティによって、まったく新しい市場の可能性が広がっています。
これまでの非鉄金属の超音波溶着の「悩みのタネ」は何だったのでしょうか?
André Deponte: 既存のソリューションでは、金属と金属が接触するため、プロセスが安定せず、工具の摩耗が激しいというのがお客様の悩みでした。プラスチックのように超音波の減衰がないため、研磨性が高いのが特徴です。経験則としては、材質にもよりますが、鉄製のホーン(溶着ツール)の場合、10万ショットで摩耗し、交換が必要になるようです。つまり、製品寿命が2週間ということになります。ツール交換や起動の時間が長いことを考慮すると、貴重な生産時間が失われ、コストのかかる廃棄物が発生します。同じレベルで重要なのが、粒子の発生を抑えることです。溶着中に発生する粒子が少なければ少ないほど、短絡のリスクが減り、生産時の安全性が高まります。
ハーマンでは、メタル溶着用の装置を2種類開発されましたね。どういった点が新しいのでしょうか?
André Deponte: 当社では、「悩みのタネ」を解決するため、試行錯誤の末、プロセスのパラメーター化と可視化を進めました。プロセスを正確にコントロールできれば、安定して、粒子が発生しないようになることがわかりました。そこで、エネルギー量とダウンタイムの相関関係を研究しました。ツールの耐用年数を伸ばしたいので、セットアップ時間を短縮するツール交換システムを開発しました。従来のツールの交換時間は最大2時間でしたが、その時間の大幅な削減を目標としていました。目標は10分。これはかなり画期的なことです。装置やモジュールをコンパクトに設計し、直感的な操作性を実現するため、設計に時間をかけました。
ハーマンの市場参入の戦略を聞かせていただけますか?
Thomas Herrmann: 近く、2種類の装置を発表する予定です。いずれもスポット溶着機と呼ばれるものですが、バッテリー専用に開発された装置とケーブル端子用の装置です。私たちが目指すのは、お客様に付加価値を提供することです。これは、コンサルティングの段階で始まっており、プロセスコントロールの改善から迅速で再現性のあるツール交換まで、広い範囲で対応します。現在はフィールドテストの段階ですが、高い目標を設定しています。最初のお客様から受注を受け、すでに準備は整っています。