生産効率を飛躍的に向上させるコンパクトシリーズ
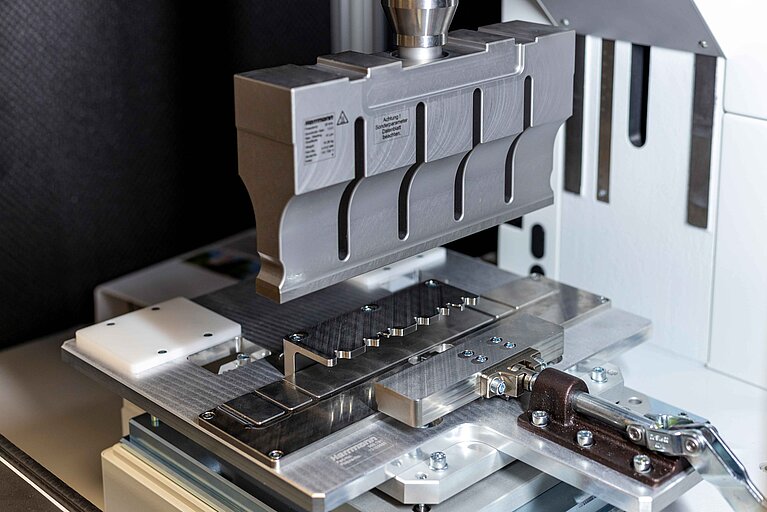
少量多品種の製品群を超音波溶着機で経済的に生産
たとえば、18個の真鍮製メス型コネクタをコントロールユニットのプラスチックフレームに挿入する場合は、すべて手作業なので、手間とコストのかかる作業でした。超音波溶着は、サイクルタイムを大幅に短縮する効率的な代替手段であり、ユニット数が少ないにもかかわらず、経済的な面でも有効です。ここでは、ホーンの汎用性とHERRMANN ENGINEERINGが重要な役割を果たしています。
apra-plast(Kunststoffgehäuse-Systeme GmbH)社では、1つのパーツにつき3分以上の作業時間が必要で、プラスチックフレームの取り付け作業は、時間のかかる作業として認識されていました。サイクルタイムが長くなるのは、合計で18個の真鍮製メス型コネクタを熱でフレームに取り付けなければならないからです。ユニット数が少ないため、自動化プロセスではコスト的にメリットがありません。また、メス型コネクタをモールド成形する代替プロセスは、コストが高く、現実的ではありませんでした。
Herrmann Ultraschallは、apra-plast社とのやり取りの中で、この課題を知り、効率的なプロセスのアイデアを提案しました。当社とのコラボレーションにより、カスタマイズの超音波溶着ソリューションを開発しました。結果:パーツの製造時間が大幅に短縮され、プロセス全体の効率が向上しました。
カスタマイズのブレードホーンで、5倍のスピードを実現
必要なのは、複数の真鍮製メス型コネクタを超音波でポリカーボネート製フレームに同時に挿入するという作業です。このプロジェクトに当たって、まず、すべてのメス型コネクタを同時に、フレームの片面ずつに正確に挿入できる特殊なホーンを開発しました。従来、フレーム全体で必要だった作業を18段階から4段階に減らすことができたため、サイクルタイムは40秒弱と、当初の5分の1に短縮されました。
溶着プロセスでは、フレーム全体の片面にある真鍮製メス型コネクタすべてに、ブレードホーンが同時に適用(照射)されます。メス型コネクタが、超音波の刺激を受けて振動します。この振動がプラスチックのフレームに伝わり、溶着プロセスが開始されます。メス型コネクタのくぼみに溶けた材料が流れ込み、接合部が固定されます。これで、真鍮製のメス型コネクタがフレームに完全に埋め込まれると同時に、素材の損傷を防ぐことができます。ビジュアル的にも完璧な仕上がりになります。
溶着プロセスでは、完成品であるコントロールユニット用のフレームをカウンターパーツに組み込むため、メス型コネクタは完全かつ均等に挿入されている必要があります。メス型コネクタの突起物などで表面に凹凸があると、後からプラスチック筐体の両方のパーツを繋ぎ、シーリング(封止)することができません。
メス型コネクタを均一に挿入するには、溶着時に機械の中で部品が完全に平面になるように設置して、動かないように固定する必要があります。このため、溝付きの専用治具を開発しました。これで、パーツを治具にしっかりと挿入してクランプし、フレームの第1面を溶着することができます。その後、パーツを裏返して再度固定し、フレームの第2面を溶着します。18個のメス型コネクタすべてが、合計4段階の手順で埋め込まれます。プロジェクトの開発プロセスにおいて、カスタマイズ設計のホーンと治具を組み合わせることで、長さ310mmのエッジを持つ長いフレームを溶着する信頼性の高いプロセスが実現しました。
さまざまな用途に使えるマシン
超音波溶着装置の償却期間を短縮できるよう、Herrmann Engineeringチームでは、apra-plast社の現在のプロジェクト以外にも、用途の可能性が広がる提案を行いました。溶着ツールのクイックチェンジシステムにより、超音波溶着装置はわずか数分で別の用途向けに再設定することができます。また、フレームと連動したプロジェクトも実施し、こちらも少量のシリーズで生産しました。
この製品は、測定器のプラスチック筐体に、プレキシグラス(PMMA)製の検査用ウィンドウを埋め込んだものです。これまではパネルを手作業で貼り付けていたため、さまざまなデメリットがありました。完成品の機能を完璧にするには、構成部品間の接続は防水加工を施す必要があります。しかし、接着剤で接合した場合、気泡が入ることが多く、気密性が失われます。また、手作業で取り付けていたため、パーツの位置ずれも起こり、気密性だけでなく、外観も悪くなるという問題が発生しました。
初回のテストで、超音波を使用することで、製品の品質が著しく向上することが明らかになりました。検査ウィンドウは超音波溶着でプラスチッ筐体に接合されるので、厳密な気密性を実現します。また、接着剤を使用しないので、ビジュアル的に美しい仕上がりで、添加物を使用しない環境にやさしい接合が実現します。超音波溶着技術を導入するもう一つの重要なポイントは、プロセスモニタリングの可能性でした。一つひとつの溶着プロセスを綿密に監視・検証することで、これまでにないレベルのプロセス信頼性が実現します。
成功要因:トレーニングとコンサルティング
今回開発した2つのソリューションにより、apra-plast社は初めて超音波溶着技術を導入しました。決め手となったのは、超音波溶着に関する徹底した基礎トレーニングが受けられること、そして、プロジェクトの金銭的・技術的な実現可能性に関するコンサルティングが提供されたことでした。マシンをレンタルすることで、お客様は実際の生産条件で社内テストを実施でき、事前に使用方法に慣れることができました。
結論
開発された溶着ソリューションを見ると、超音波溶着なら小ロットの生産でも無理なく対応できることがわかります。ただし、プロジェクト期間にわたって綿密なサポートを行い、汎用性の高いマシンを開発することが条件です。特に手作業での接合と比較すると、超音波溶着は生産時間の短縮と製品の品質向上という大きなメリットがあります。つまり、お客様は、経済性、持続可能性、効率性の高い製造プロセスを設計することができるのです。